by Webmaster | Feb 17, 2014 | News
The Freeze-Thaw Cycle
What the harsh 2014 frost means for your pavement.
This year began with a rough winter as well as some of the worst frost the Midwest has seen in years. Weather this cold can wreak havoc on your pavement, causing trip hazards, potholes and sewer/catch basin failures.
When moisture permeates your pavement and freezes, it creates an Ice Lens. This Ice Lens pushes the pavement upward, creating cracks as well as walking hazards. With frost the worst its been in years, this moisture can cause serious damage to your pavement once it thaws.
The full effect of frost on your pavement is shown in the graphic below. Treating pavement damage immediately is vital to extending the life of your pavement and reducing issues in the spring. Contact a Rabine Group representative to learn how you can protect your pavement.
by Webmaster | Jan 10, 2014 | News
Pavement Solutions recently donated their time, money and hard work to completing a striping and sealcoating project for the Richmond Fire Department. Pavement Solutions, a Rabine Group company, understands the importance of Corporate Social Responsibility and giving back to the community.
Corporate social responsibility is a way of incorporating ethics and self-regulation into the corporate business model. Rabine Group uses our foundation to encourage and implement this idea of corporate responsibility by using our successes to support our local communities.
by Webmaster | Dec 17, 2013 | News
The Senior Vice President of Global Engineering at Rabine Group was recently named one of ICSC and Centerbuild’s 20 Under Forty list. Ryan spearheads pavement engineering, maintenance and innovation at Rabine Group, including green solutions, asphalt mix designs, Rabine Pavement Management and more. Ryan is a LEED accredited professional and an active board member on the Rabine Group Foundation, Rabine Group’s nonprofit organization. Ryan’s passion, knowledge and experience make him an irreplaceable member of the Rabine Group team.
Centerbuild’s 20 Under Forty recognizes leaders and innovators in the retail building and construction industry. For more information on ICSC, visit www.icsc.org.
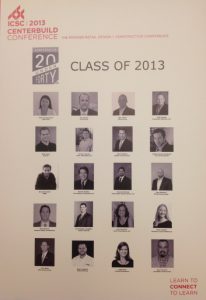
by Webmaster | Nov 10, 2013 | News
This year, Rabine Group employees put together a ‘Giving Tree’, a collection of gifts to be donated to WINGS, a support center for homeless and abused women and children throughout Chicagoland. This year, Rabine Group provided gifts for 65 people to be delivered just in time for the holidays.
To learn more about WINGS and how you can help, visit www.wingsprogram.com.
by Webmaster | Nov 7, 2013 | News
In today’s economic conditions, retailers are faced with many challenges including reduced overall funding, restrictions on sizes of projects, increased scrutiny over the quantity of bidders and a slow, steady rise in prices due to material and labor fluctuations. One of the most commonly overlooked or under-considered factors property managers and facility owners experience with their pavement maintenance and capital improvement programs is quality management.
Some owners and managers utilize consultants to audit and measure the performance of their contractors through quality assurance (QA) programs. Others utilize testing firms to perform periodic samples of testing while their contractors perform work. Many take the approach — after an extensive vetting of their preferred contractors — to make a decision based primarily on the competitive prices they receive and rely on the contractor’s quality control (QC) program. While there are many different ways to measure and manage QC/QA programs, there are several effective strategies to focus your efforts when evaluating your asphalt paving programs. Those strategies include: material selection, equipment selection, compaction and construction testing. Let’s first begin by identifying what quality control is and why it is important to you as facilities professionals.
Quality Control (QC)
Quality control represents the activities and measures a contractor takes to manage a project and deliver the results that are specified and expected. Quality management begins on a project well before a contractor starts the construction project on your facility. Factors such as the materials specified for use on the project and equipment selection have significant impact on the success or failure of a project as well as long term operations and maintenance costs. Your paving contractor should manage these factors, among others, in the form of a QC program while constructing asphalt or concrete pavements.
Material Selection
The correct mix design has a significant impact on the cost of a project as well as the longevity of the product throughout its life cycle. It is not uncommon to see mix designs specified for new construction as well as maintenance activities from engineers and consultants that substantially exceed the requirements of the project. These mixtures are the ones utilized on roadways, taken directly from state specifications because the engineers are used to designing public improvements and not parking lot improvements. These DOT mix designs are designed around much higher volumes of traffic and, when they don’t receive the frequency they are designed for, underperform and don’t last as long. Most asphalt plants have developed alternate mixtures designed around lower volumes of traffic and vehicle sizes known as commercial mix designs. Commercial mix designs should be specified to achieve balance with finished surface appearance, traffic loadings and cost. The correct mix design will save as much as 10% of the overall cost of a project and will perform better throughout the life of the parking lot.
Equipment Selection
Having the right equipment on a project can be a difficult thing to measure or analyze from an owner’s perspective. Paving equipment should be self-propelled, capable of placing materials at uniform depths and widths in excess of 12 feet. Pavements are constructed in consecutive passes parallel to each other and the weakest points in the pavement are always where the passes of the paver are joined. These joints are the first to crack and are commonly maintained throughout the life of the parking lot with crack sealing. When undersized paving equipment is utilized, the paving width tends to be narrow (typically 9 feet instead of 12 feet to 14 feet), creating more joints. This can translate to increased life cycle management costs for the owner/manager in the future as referenced the example below.
Compaction
Compaction equipment plays a significant impact in the quality and longevity of a pavement project. Asphalt is typically delivered at temperatures in excess of 300 degrees Fahrenheit; when placed through a paver and compacted, it achieves an optimum density (compaction) within a specified range based on DOT specifications. The temperature at which the material is delivered determines the time that the contractor has to properly compact the product. If the material is too hot or compacted too soon, it will leave roller marks in the form of lines on the pavement. In this example, the pavement, while constructed well and properly compacted, will be aesthetically challenged and lead to dissatisfaction with the final product. Additionally, these roller lines often translate to small puddles in parking lots preventing stormwater runoff from reaching the sewer system. If the material is too cold it will not compact properly and will be weaker than it is supposed to be when finished. In this case, the surface may appear coarse or rough, may not be bonded properly leading to raveling (loose stones on the surface) and could additionally be not fully compacted, leading to a reduced life cycle requiring removal/replacement and an accelerated timeline for resurfacing.
Quality Assurance Example
A 50,000-square-foot parking lot is milled and resurfaced by a contractor at 9-foot widths instead of 12-foot widths for $1.50 per square foot, which equals $75,000. This reduced width translates to over 1,000 feet more of joints created in the parking lot. It is these joints that require crack sealing and over time typically become areas of fatigue (alligator) cracking. Assuming an average cost of $0.65/LF for crack sealing, this would equal an additional $650 per event, which when multiplied by five applications equals $3,250. Additionally, projecting these costs forward to failure in fatigue cracking, assuming an average cost of $3 per square foot for removal and replacement, we can determine the additional cost of replacement: 500 additional LF x 10 feet wide equals 5,000 square feet of pavement replacement equals $15,000. So, in this example, not having the correct paving equipment on a resurfacing has a life cycle cost of $18,250 — or 25% more maintenance expense compared to initial cost because of improper equipment utilization. If your parking lots are larger or smaller, the net impact is roughly proportional and when multiplied over hundreds or thousands of stores will drastically impact your maintenance budgets for years in the future.
Quality Assurance (QA)
Quality assurance represents the activities and measures that are conducted to ensure that the QC measures are effective and working to achieve the desired results. When maintaining a large quantity of parking lots spread out regionally or nationally, it can be difficult to efficiently and effectively manage the facilities and measure the quality of construction activities. Some property managers and facility owners have outsourced consultants to supervise construction and others rely on the contractor’s judgment and reputation to protect their investments. Both approaches are effective, but these strategies either expose the decision maker to risk in compliance with specifications relying on their contractor alone or reduce their operating budget and ability to maintain their pavements through payments to consultants and testing firms. There are two simple strategies that can be easily employed by the property or facility manager at minimal expense and resources. These approaches audit quality from an owner’s perspective that promotes accountability and compliance with specifications and scope of work (SOW).
1. The total quantity of materials required for import (delivery) and export (removal) on any project can be easily calculated using standard conversions for volume (areas multiplied by depth) to weight (tons, cubic yards, etc.). As property or facilities professional, you can require that copies of material tickets, properly labeled and coded from each project, be assembled and submitted upon completion. This provides a means of measuring whether or not the contractor installed the proper quantity of materials and whether or not the finished product will meet or exceed the specified depth on the SOW. Any reduction in thickness below specifications will reduce the life cycle and longevity of the product leading to earlier pavement maintenance and future rehabilitation projects.
2. Post-construction testing of your properties for larger capital programs is an excellent way to audit the quality outside of quantity measurements to manage quality. Testing of asphalt pavements typically require consultants or engineering companies to be contracted. In some instances there are quality self-performing contractors that have the ability to conduct this type of testing in-house. By enabling a program of testing to include compaction testing and pavement coring, you will ensure that the pavement is built properly and consistently as well as audit the thickness of the pavement. Upon completion you will receive a report detailing the compacted thickness of the pavement and the level of compaction achieved for each area tested. This form of testing will ensure that you are measuring the quality in the field, allow you to quantify the quality of construction, and hold your contractors accountable for their work — whether they self-performed the job or utilized a network of subcontractors. These types of programs do not need to be mandated for all projects and are often best implemented at a random frequency to get a true representative sampling of your project sizes, locations and contractors performing work.
Measuring quality is challenging and often overlooked, but is critical to the long term success of any pavement management program. Having a QC and QA program in place will maximize your results and instill accountability in your contractors while providing reassurance that your properties are achieving the maximum value of the improvements and investments you are completing.
Recent Comments